Hi Johnson
was a well-known designer and manufacturer of model airplane engines in the middle
of the last century. His series of throttled engines was widely used in the early
years of radio control. A lot of research went into producing the engines to produce
long lifetime, easy starting, and consistency of operation. The Johnson 35 R/C,
which is the subject of this 1962 American Modeler magazine article, was
one of the first to used dual ball bearings on the crankshaft, contributing mightily
to the accomplishment of the aforementioned goals. The state of the art for all
types of model flying had advanced to where pilots could expect their models to
last longer (not as many destructive crashes) so extending engine life was needed. Powerplant Revue: Hi's Radio Mill Proves Potent Yet Docile .35
Many powerplants in the .35 size look pretty
much alike. And the Johnson J-R/C from outward appearance is not unlike other 35's.
But mount it, flip the prop a couple of times and you find it's in a class by itself.
This .35 is one of the smoothest, easiest starting, cleanest running engines
tested, regardless of size. Not once during the entire running period was it necessary
to prime the engine. Nor was it necessary to readjust the needle valve from its
best setting of 1/4 turn open. Starts, hot or cold and exceptionally fast, required
only a one flip choke, then one or two flips to catch.
Cleanliness of operation, or more technically combustion efficiency, puts the
J-R/C way up there. At about 3/4 throttle (9,500 rpm) 3 ounces of K&B Supersonic
100 fuel ran this engine for over 7 minutes.
The J-R/C cannot be considered a quiet engine by any stretch of the imagination.
Standing close to it, even in an open field, can put your head to ringing. This
high noise factor may even be helpful to the R/C pilot who wants to hear that his
engine is running smoothly at idling position.
Much as we'd like to give an absolutely perfect report to a deserving product
we did experience some difficulty with the needle valve supplied. When turned in
to what should have been a fully closed position, our test engine was still able
to draw fuel. In fact, with a pressurized fuel tank it could not break out of a
rich running 4 cycle. It was therefore necessary that we conduct our test without
using a pressurized fuel supply. We have since learned that this condition is not
common to all J-R/C engines. We agree with Hi Johnson that numerous factors can
affect carburetor performance, (temperature, fuel, humidity, altitude) and that
it is nearly impossible to produce a single carburetor for all conditions. Available
through local hobby shops is Part Number 1524 which consists of three differently
tapered needles; one of which should give you optimum results. Without a pressure
tank our test engine was very critical on tank position. A drop of only a few inches
had serious effect on performance. Should this same condition be present in your
J-R/C, get yourself a set of these needles and experiment until best results are
obtained with a pressurized fuel system.
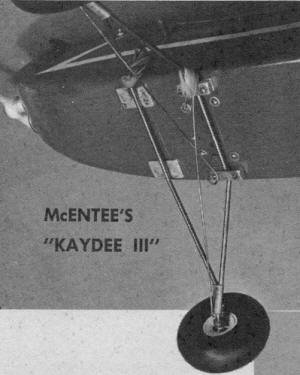 McEntee's "Kaydee III"
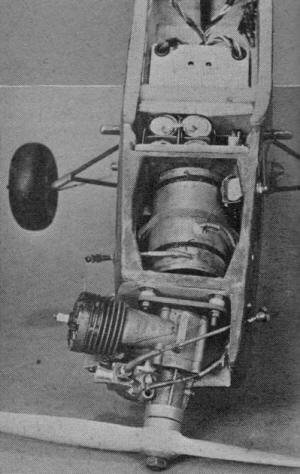
Last issue, data and plans for Intermediate R/C winner. Herewith more pix. On
aileron note lead balanced wire yoke. Battery pack slide shows charging socket at
near corner. Angled double wire on stab is static balance. Tail wheel's under its
pivot point.
|
Internally, the J-R/C is fairly conventional, yet its designer has gone all out
to insure long engine life. The use of instrument, precision ball bearings requires
more care as to cleanliness but this is repaid by the extended life built into them.
The steel cylinder is hardened by a special process that makes it tougher than hard
chrome.
Because of. its self-lubricating properties, Meehanite has come into prominence
as a piston material in miniature engine manufacturer. But to increase lubrication
between cylinder and piston, Johnson hit upon a rather ingenious method. By using
an extremely porous type of Swedish Scintered Meehanite the fuel and oil usually
trapped inside the piston is forced through its walls to the cylinder barrel. To
prevent a porous dome which would affect compression, both the inside and the outside
of the dome is impregnated with a plastic composition which, when burned, forms
a tough crust which completely seals it. Five hours of running time is required
for the sealing process to take place. At the time of writing, life tests of these
engines were still going on. We're informed that mills picked at random from the
assembly line were still going after 304 hours continuous running .
The cylinder barrel with its oversized intake port is a push-fit into a die-cast
aluminum crankcase. A die cast aluminum head with machined cooling fins employs
six Phillips head machine screws to hold it and the barrel securely to the crankcase.
Gaskets prevent leaks.
Johnson's one-piece crankshaft is heavily counterbalanced. It utilizes a hollow
crankpin to further aid balancing. His rotary port is exceptionally large - almost
1/2" square. Two Fafnir ball bearings are employed. A large one, within the crankcase
has 5/8" inside diameter contains 21 balls. The smaller is mor3 conventional with
1/4" inside diameter and 5 balls.
Propeller drive is the friction type. An aluminum split tapered collar hugs the
crankshaft and the tapered inside diameter of the aluminum drive washer when tightened
by the prop nut grips this collar and squeezes it snugly to the shaft. No prop slippage
was encountered during our test period.
Connecting rod is forged aluminum. Wrist pin is steel and padless. Crankcase
rear cover, die-cast aluminum, comes fitted with a removable pressure tap. If a
pressure tank is not required, a machine screw (supplied) replaces the pressure
tap fitting.
The secret to the broad running speed range credited to the J-R/C is its AM-1
carburetor. This automatically provides a proportioned mixture of fuel and air throughout
the entire speed spectrum. Found extremely reliable and simple to adjust even while
the engine is running, its actuating arm may be rotated to any convenient position
and then locked in place. Full travel of the arm, from high to low speed, is approximately
1 3/8".
Performance tests were conducted as soon as the engine would run out a complete
tank of fuel at full speed without slowing down or showing any sign of overheating.
This required a little over 1 hour of 4 cycle running.
With a Top Flite 11/6 our test engine hit 13,000 rpm and idled smoothly at 1,800
rpm. An 11/4 and a 10/6 registered the same high of 14,500 rpm and low of 2,000
rpm. With a 9/6 nylon prop speed jumped to just over 16,000 rpm as idling speed
increased to 4,500 rpm.
At the end of the test period, the engine was disassembled and inspected. No
sign of wear was discernable. In fact, the piston had not completely seated itself.
A rather crusty residue had begun to form on the piston dome but had not completely
covered it. The underneath portion of the dome was only partially uncrusted. From
this we conclude that when the dome becomes completely sealed full compression ratio
is reached and higher power results.
Specifications: Bore .770; Stroke .770; Disp. .358; Compression ratio, 10.8:1;
Weight, 9-oz. Manufacturer: Dynamic Models, Inc., 13755 Saticoy St., Van Nuys, Calif.
Articles About Engines and Motors for Model Airplanes, Boats, and Cars:
|