How
can it possibly be that it was in 1957 that Cox introduced the
Babe Bee .049 engine?
That pre-dates me by a year, and man, I'm feeling old. Cox must
have sold 10s of millions of the beauties. I know my paper route
earnings were responsible for at least half a dozen of them. Today,
a new-in-box (NIB) version will easily cost you $100 on eBay. Alas,
what was music to our ears was annoyance to the neighbors, so now
electric motors have replaced the little screamers on toy store
shelves. I tell Melanie if I am ever unconscious and one of these
two things does not rouse me, pull the plug: the sound of an .049
engine running, or the smell of a spent Estes rocket motor. Babe
Bee: New Member of the Cox Family
Back in the early 30's when the silence of rubber powered model
flying was first shattered by the roar of the model gas engine,
more flyers dreamed of owning one of these noisy monsters than could
actually afford the cost. For $21.50 was a lot of money in those
days and that was the cost of the engine alone.
To get the engine running you still needed an ignition system
consisting of a coil, condenser and batteries, which meant an additional
$5.00: Propellers weren't cheap either and they broke just as easily
then as now.
Construction of a gas model became a club project with members
chipping in to pay for the engine and the cost of building the model.
And speaking of models, 9 and 12 foot jobs were not considered too
large!
By comparison, today's model builder profiting by. the advancement
of mass production methods and keen competition among engine manufacturers
can own the newest member of the amazing Cox family of engines for
less than the price of the outmoded ignition system alone.
The Babe Bee, one of the lowest priced model engines available
today, is the result of the mass production skill of its manufacturer,
L. M. Cox Mfg. Co. of Santa Ana, California.
Mass production can usually lower the cost of machining a complicated
piece of equipment but simplification of design and the reduction
of the number of parts necessary to do a specific job is frequently
more practical.
The Babe Bee is the first engine in the Cox series with a simplification
of the original induction reed design. Basic design of major components
follows the Space Bug Jr. but with some modifications. which great1y
change outward appearance. Aluminum crankcase although less fancy
is stronger than those previously used. It is also approximately
1/8" shorter to the propeller. Fuel tank is machined from aluminum.
Forward portion of the tank forms the crankcase backplate and
also houses the induction valve. This valve consists of a single
extremely thin piece of flexible bronze actuated by crankcase compression.
It is held in place by a steel wire snap ring which also limits
its amount of travel. The rear of the tank is an aluminum casting
which includes the needle valve assembly and the radial mounting
lugs.
The needle valve has been moved to the top of the tank where
it is exceptionally easy to get to. Air intake tube still located
through the center of the tank has been redesigned to save drilling
a hole through the motor mount to allow air to reach the needle
valve. With the motor mounted flush to its mounting surface air
can reach the needle valve via a recessed slot cast into the rear
surface of the tank assembly.
The steel crankshaft is hardened and ground to a smooth finish.
By relieving the center of the shaft, friction due to oil drag is
kept to a minimum. Instead of the one piece crankshaft used in previous
Cox engines, the Babe Bee's is internally threaded at its forward
end to receive a propeller screw. This feature has been proven on
many other engines to practically eliminate bent crankshafts even
under the most severe crash conditions.
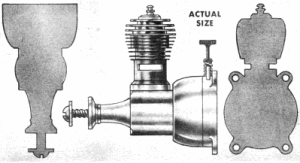
The steel cylinder employs the same porting design as used on
the Space, Bug Jr. - a single transfer port located between the
two exhaust ports. Cylinder head and glow plug unit is standard
Cox design as is the design of the hardened and ground piston and
its ban and socket type aluminum connecting rod.
Engine purchased for tests bears out the manufacturers claims
that no break-in period is required.
Using a 5-1/2" dia. 2-1/2" pitch plastic propeller our test engine
started with the very first flip and reached maximum rpm of 16,000
on the first tank of Thimble Drone fuel. No needle valve float was
encountered anytime during test period; quick starts were consistent
whether the engine was hot or cold.
Due to the type of fuel induction used, the Babe Bee will run
in either clockwise or counter clockwise rotation. This can be an
advantage as it allows the experimenter to design pusher-type models
or counter-rotating multi-engined models.
Best starting method for this type engine consists of a good
prime ' directly into the exhaust ports and a real snappy flip in
the direction .of rotation you de-sire. It was found that a half-hearted
flip resulted in starts -in the opposite direction. If you should
encounter opposite starting difficulties try flipping the propeller
opposite to the correct direction of rotation. We tried this idea
out several times during the test and it worked perfectly.
Other Cox / Thimble-Drome Articles:
•
Thimble-Drome
Piper Super Cub 105
Articles About Engines and Motors for Model Airplanes, Boats, and Cars:
Posted January 17, 2013
|