The old saying about the pioneers taking the arrows might be a little frowned upon in today's overly sensitive society,
but it is apt when considering the trials and tribulations endured by early adapters of electric powered flight.
Compared with today's extremely high energy density lithium polymer (LiPo) battery packs, the old nickel cadmium (NiCad) batteries were
impotent, heavy, and bulky. Nevertheless, guys like Kenichi Mabuchi forged new frontiers (continuing with the pioneer theme)
that got people thinking about the benefits of powering models with silent motors and batteries rather than with noisy engines
and their required messy fuel. This c1974 article from American Aircraft Modeler magazine reports on one of
those early efforts.
Electromotive Power Plants
Whether it be a revolution in terms of noise or the energy crisis, major manufacturers are striving to provide modelers
with a new way of doing our thing.
by Larry W. Hoffman
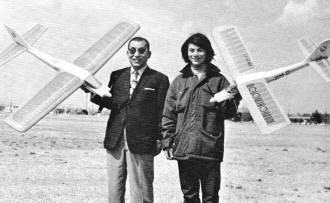
Kenichi Mabuchi (left) and author's son, Kenji, hold prototypes of electric-powered models. Mr. Mabuchi's
model is a full-house bird, while Kenji's is three-function. Note large props and air scoops.
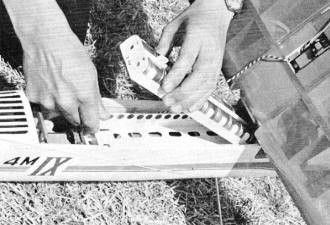
Power system installation is a snap-in battery tray. , or they can be transferred intact to the cabin
of the multi.
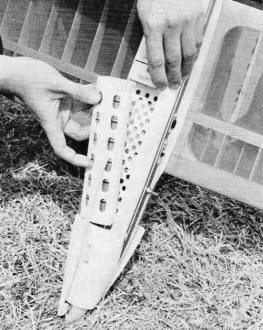
Fourteen batteries drop into the well-ventilated access hatch of the glider.
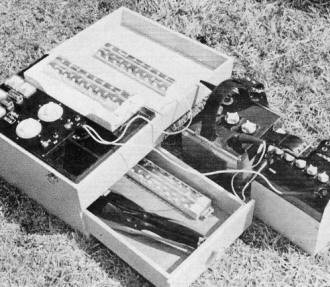
Charging modes are either elaborate, where the master charging unit can charge several battery trays
simultaneously...
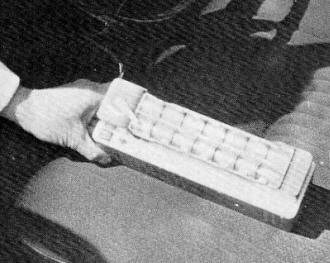
...or the simple portable charger which operates off the car cigarette lighter.
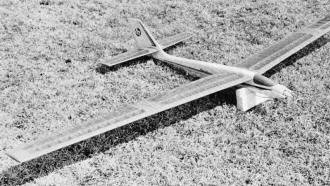
Two adaptations of electric power. Glider has folding prop to clean things up for better duration.
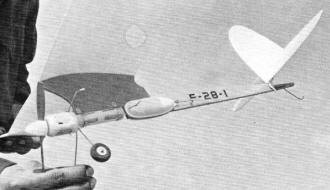
The free flight model is compact and sports a dethermalizer module.
Lately, it has become old hat to hear about modelers the world over losing their flying sites because of excessive noise.
It is equally common, however, to hear about the many interesting and constructive muffler designs currently under development.
Even better mufflers are needed to get around this insidious problem of noise pollution.
Articles and bits-and-pieces of information relating to an adjunct to the hobby/sport of radio control flying have appeared
in trade journals. Although not a new idea, Electric Powered Flight offers the path of least resistance around the noise
difficulties we all face. The biggest problem with this form of propulsion has been the tremendous power required to drive
our flying machines around the sky at regular speeds and for the durations to which we are accustomed using our present
power plants.
Work is undoubtedly underway in many countries to develop electric power plants efficiently and economically. However,
many are probably not aware of the efforts being made in Japan by the world's leading manufacturer of miniature DC motors,
the Mabuchi Motors Company.
American modelers are familiar with the Mattei SuperStar that operates with electric power from rechargeable batteries.
The motor for this plane is made by Mabuchi. It is one of many with which they are presently experimenting to realize the
technical requirements for greater duration and power. During a visit to the Mabuchi factory near Tokyo, I was treated to
a complete tour of the manufacturing facilities and the experimental laboratory Mr. Mabuchi has set up for building and
testing motors and planes.
The factory is a modern structure built within the last three years. Along with two other factories in Japan and one
each in Taiwan and Hong Kong, the total daily output of miniature DC motors is approximately 800,000 units. Sixty percent
of total production feeds the export market, where motors go into the automotive industry's electric windows, windshield
washer pumps, consumer electric appliances such as rotisseries, camper water pumps, hair dryers, etc. And of all the motor
driven toys made in the world, Mabuchi's DC motors are installed in 75 percent of them.
One of the reasons for the large demand for Mabuchi's motors is consistent quality and acceptable cost. Quality control
is at a high level; each and every motor receives several operational tests during final stages of completion. The machines
which assemble the motor shaft to the armature core were designed by Mabuchi engineers and are electronically controlled
to prevent improper assembly and to speed production.
Armature coil winding is semi-automatic with electro-mechanical controls for accurate measurement of the number of turns
wound on each segment of the finished product. Soldering leads to the commutator and final assembly/testing is done by hand
by specially trained workers.
Mr. Mabuchi demonstrates the quiet thrill of electric flight with his three-channel model. Note that no one is holding
his ears!
A hidden element that goes a long way to making a high quality product are the efforts of management to make the workers
more comfortable and happy on or off duty. Dormitories are provided with swimming pools and an assortment of athletic equipment.
All work areas are kept neat, clean and well lit. Paying attention to the workers' personal needs pays off. Employees give
greater attention to production quality requirements.
In the experimental lab, there is a vast array of equipment used to make planes, cars and boats, and motors to power
them. Mr. Mabuchi employs five engineers with electric/electronic and mechanical experience to provide test beds for checking
the power pack and motor combinations. They are in search of the best input/output power combinations.
One of the results of their efforts to be marketed soon is a motor, prop, two-cell battery with holder and charger for
free flight planes. A variety of FF configurations have been developed by the Mabuchi technical staff for test purposes;
however, the company does not plan to make anything but the motors. With the help of kit manufacturers it is hoped that
a combination can be worked up for retail sale, but a definite schedule has not been decided on as of this moment.
After a flight, the rechargeable cells are placed in the portable charger and a built-in timer is set to maximum. Two
min. later the top opens, automatically releasing the fully-charged cells for use. Power for the charger is four lead-acid
motorcycle batteries.
The radio-controlled planes use one, two, three and four channels of digital proportional radio equipment, with the larger
ships wired to operate completely by radio control. To control the motor on and off, reverse direction, vary speed and operate
all control surfaces, one must simply turn on the receiver-transmitter switches. All experimental aircraft are constructed
from standard building materials such as balsa, hardwood, polystyrene foam and Mono-Kote.
The motor glider uses a folding prop to reduce drag. And, if the landing approach doesn't satisfy the pilot, he simply
switches on the motor, lines up for another pass and puts it down just where he wants it! What does this portend for the
future of spot landing contests!!??!!
All the data on the Mabuchi fleet of planes is not in hand - the following is all that has been made available: Glider
- Model No. MG-2 - 1.8 kgs (about four lb.). Four-channel - Model No. 4M-9 - 2.3 kgs (five lb.). Two-channel - Model No.
2M2-4 - 1.4 kgs (three lb.).
Fourteen and 18 cell battery packs are used, each charging at six to seven amps for approximately ten min. Discharge
current runs close to 15 amps, giving approximately four min. of running time. However, cooling air is required to keep
the motor from overheating.
Right now the Mabuchi Motor Co. is experimenting with a new ferrite magnet that could reduce motors to half their present
size with increased power and less current drain. Who knows? With all the development going on, electromotive power plants
for RC planes might just be right around the corner!!!
Editor's Note: Astro Flight, Grauper and Galler Industries' electric systems are already available in the U.S.
Articles About Engines and Motors for Model Airplanes, Boats, and Cars:
Posted May 29, 2016
|