Balsa wood was a special thing to me as a kid. To me, it represented the essence
of model airplanes and model rockets. At the time - the 1960s and 70s - plastic
and foam as model components were considered a sign of cheapness, low quality, amateurishness.
It was like having "Made in Japan" stamped on it. Now, of course, it's a different
world where Japan is renowned for some of the highest quality electronics and cars
and the plastic and foam ARFs represent some of the highest-performing aircraft
at the flying field. I have owned a few of those foamies, but still, at least for
my tastes, nothing beats the look, feel and aroma of balsa. Somehow the tell-tale
surface texture of foam, even with a nice paint job, ruins the authenticity of an
otherwise beautifully factory-finished scale F4-U Corsair or P-38 Lightning. Sorry,
that's just the way it is. Sig Manufacturing was, in the aforementioned era, one
of only a couple major balsa suppliers (Midwest being the other). The Sig catalog
had a really nice primer on balsa with a treatment of history, tree harvesting and
production, and technical information like density of balsa sheets, sticks, and
blocks. That information from an early 1970s catalog is reproduced here. I also
have a page on balsa wood density
and weight, and a reproduction of an article on
balsa tree foresting and
harvesting by Sig Manufacturing from one of their 1970s era catalogs.
Important Facts About Balsa Wood
For people who like to know everything!
Courtesy of International Balsa Corp.
What Makes Balsa So Unique?
Balsa is the softest and lightest commercial wood in the world. It weighs only
4 to 18 lbs. per .cubic ft., averaging about 9 lbs. per cu. ft. But pound for pound,
it is stronger in some respects than pine, hickory or oak - it is one of the strongest
woods in the world for its weight, particularly in tension. It is resilient - with
high compressibility and recovery. It is buoyant - 1 cu. ft. will carry over 50
lbs. of water. Its high insulation value is equal to cork. Balsa's high electrostatic
qualities make it an insulator against electricity. Balsa absorbs shock and vibration
well. It is inert - no fumes, dust or reaction. It is stable and will not warp readily.
It is durable - withstanding heat, cold, dampness long storage and weathering. Balsa
is easily workable and can be processed with the same tools and techniques as ordinary
woods. Balsa can be processed to simulate many other materials and takes these finishes
and processes well.
The "Friendly" Wood
Most people like wood anyway. It has such a friendly feel. But Balsa has this
"friendliness" to a higher degree ... it is pliant to the will of man, so light,
so soft, so easily worked into so many things. Lay a piece of Balsa before a man,
woman, boy or girl, and they can't resist picking it up, hefting it, feeling its
smoothness, pressing their finger into it to test its submissiveness. With Balsa
every person is an artisan, an artist. Balsa Wood is used so extensively in building
models of all kinds because the hobbyist has found that it will give him a lighter,
stronger job, and greater flexibility in its construction and performance, than
with any other material.
The Perfect Nurse
In this age of science, when man is always trying to improve on Nature, it is
unusual to find a substance where Nature has outdone man. People ask "What process
do you use to make Balsa so light?" There is no process. Balsa is just naturally
light. Balsa grows only in the humid rain forests of South and Central America.
Actually Nature did not design Balsa as a crop tree. While it needs a lot of moisture,
it grows only in well-drained sites. When the young seedlings of the forest giants
start to grow on the forest floor, they need a nurse tree to shade them and keep
them from drying "out in the hot tropical sun. That nurse tree must grow fast, with
a spreading crown and large leaves to provide shade for the babies.
Yet there can't be too many leaves because they would shut out air and sunlight
from their charges. While the nurse tree must grow fast, it can't put too much beef
into its body. The accent is on Volume, not on strength. And it must not live too
long .... just long enough to see the seedlings through to where they can take care
of themselves. The Balsa tree goes all out to live up to the characteristics of
a perfect nurse.
Speed vs. Strength
What happened to the wood in the Balsa
tree when it sacrificed substance for speed of growth? Under the microscope we find
the basic parts the same as in all woods - Nature is conservative in a way, and
when She finds a good, basic design, She adapts it in various ways, so that She
obtains a variety of forms. She begins with a basic material, cellulose, which weighs
97 lbs. per cubic foot. She molds it into various shapes - tubes, cells, long, tapering
fibers. So far the parts are the same for all the different kinds of wood, and if
She were to stop there, there would be only one kind of wood. But now She diversifies
- She makes one part large, the other small, She thickens the cell wall on some,
slims them down on others. She leaves a big opening here, a small opening there.
She bunches some together, others She spreads out. Here and there She adds a pinch
of salts, some crystals, pumps in some resin or tannin, and by arranging the same
few elements in hundreds of different ways, She comes up with thousands of different
species.
In Balsa, Nature has cut every possible corner to do a fast, efficient job. Everything
that would build up weight has been eliminated. The cell walls have been slimmed
way down. The spaces inside the cells have been enlarged, so that the ratio between
solid matter and space, is as small as possible. Most woods have gobs of heavy,
plastic-like cement, called lignin, holding the cells together. In Balsa, lignin
is at a minimum. The result is a wood which may weigh anywhere from 4 pounds per
cubic foot, to 12 pounds per cubic foot. (As the tree grows older, passes its prime
and begins slowing down in growth, it may develop wood as high as 18 lbs. per cubic
foot.) Compare this with one of the lightest, native woods, Spruce, which weighs
23 lbs. per cubic foot. But, you will ask, "Hasn't Nature gone too far and robbed
the tree of all its strength?"
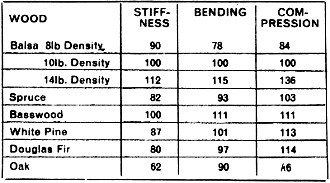
Table I - Strength/Weight Figures for Various Woods
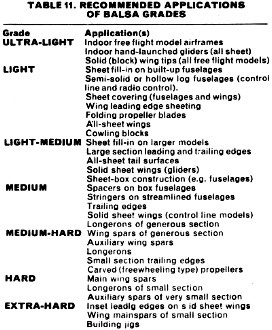
Table II - Recommended Applications of Balsa Grades
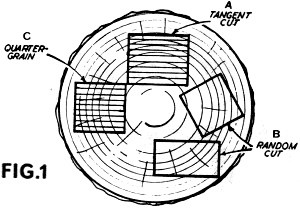
Fig. 1 - Balsa log cut types.
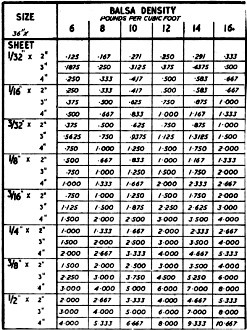
Table III - Balsa Sheet Density
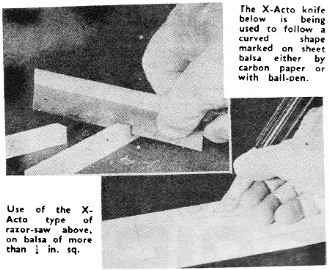
Use of the X-Acto type of razor-saw (top), on balsa of more than
1/4 in. sq.
The X-Acto knife (bottom) is being used to follow a curved shape
marked
on sheet balsa either by carbon paper or with ball-pen.
(note: these two images were printed upside-down in the catalog)
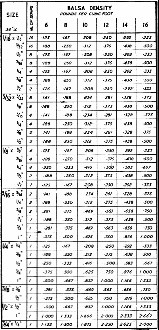
Table IV - Balsa Strip Density
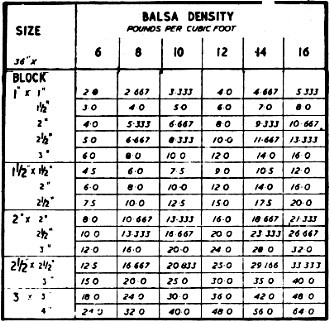
Table V - Balsa Block Density
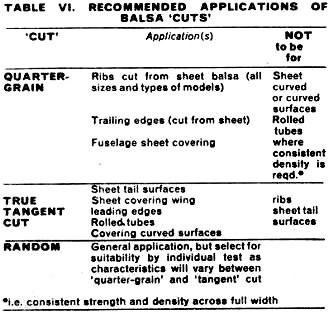
Table VI - Recommended Applications of Balsa 'Cuts'
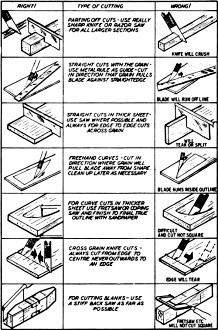
Figure 5 - Right and Wrong Way to Make Cuts in Balsa
Nature has many tricks up its wide sleeve. It has given the Balsa tree a tough,
stringy bark, which unlike many trees does not flake off but builds up as the tree
grows. She pumps the Balsa cells full of water until they become rigid - like an
automobile tire full of air. (The green Balsa Wood may contain as much as five times
as much water by weight as wood substance. Compare this with green, native woods,
which may contain only three-quarters the weight of water as against the weight
of wood.) But the most important to us is that She takes the Balsa cells and by
twisting them about each other, arranging them with consummate skill, she gives
the wood itself an inherent strength.
Romance of Logging
There is no such thing as woods of pure Balsa trees. They grow singly, or in
very small, widely scattered groups. It is a matter of finding one tree here, another
tree 100 yards over the hill. Because of the way the individual Balsa trees are
scattered throughout the jungles, it is not possible to use many of the established
logging procedures used in this country. Machinery requires a more or less concentrated
stock of logs. It also requires people who are skilled in its use and maintenance.
To the surprise of our efficiency experts, we have found that the best way to log
Balsa is to go back to the methods of Paul Bunyan. Chop them down with an axe -
no saw; haul them to the river by ox team; float them down the river to the mill
in rafts.
This procedure cannot help but bring back the old, romantic days of logging about
which so much has been written in the United States. You have the same hairy-chested
logger, maybe a little shorter than his counterpart in song and story, but still
rough and tough and hard as nails. You have the same ox skinner with his long, bull
whip and his marvelous mastery of profanity in three languages. You have the river
rats floating the rafts down to the mill and whom, for shear guts day after day,
I challenge you to match anywhere in the world. These are the men whose muscle and
blood and sweat make your model airplane.
Hurry Up, Amigo
Because of their vulnerability to attack by insects and fungi, it is very important
that the Balsa logs be taken out of the woods and delivered to the sawmill just
as quickly as possible. Unlike the logging of other timbers, you cannot cut down
a great number of logs and stack them for transportation while awaiting a propitious
time. They must be taken out of the woods immediately, preferably the same day,
and dragged to the river. They must then be floated to the mill without delay. The
best logs are received at the mill within ten days to two weeks after they have
been cut.
At the sawmill we don't waste any time with them either. The rafts are broken
up immediately arid the logs are dragged up a long ramp to the head saw, where they
are squared. From the head saw they go to a gang saw, which converts them into boards.
Importance of Kiln Drying
The next step is one of the most important in the process of manufacturing Balsa
boards. It is kiln drying, by means of which the moisture is removed from the wood.
Without kiln drying Balsa would not have its characteristic lightness, nor its strength.
Kiln drying kills bacteria, fungi, and insects; because the wood is dry it prevents
them from returning. Balsa that is not kiln dried, or improperly kiln dried, bears
very little resemblance to the finished product which most of us know. But kiln
drying is a rather fine art. For the sake of economy, the wood should be dried as
quickly as possible. but if it is dried too quickly, it may be irreparably damaged
- slits appear in the wood, and the boards twist and warp. You may have a condition
where the outside may be dry and the inside damp - this is knows as case hardening.
When a case hardening board is cut, it will twist like a cork screw.
Drying is accomplished by the application of heat through steam heat exchangers,
and through the regulation of the amount of humidity. If the heat is held at too
low a point, it may increase fungus attack instead of killing it. If the heat is
too high, it will kill the natural elasticity of the wood. If the humidity is too
low, the wood will dry out too fast, and will result in all the drying defects mentioned
before. If the humidity is held too high, the wood will not dry. The dry kiln operator
then has to walk a tight rope between the two extremes, manipulating his valves
and controls so that the fastest, most efficient drying is accomplished, with a
minimum of damage. This is done by placing the Balsa lumber, stacked in layers,
on cars with spacers between the layers, to permit the passage of air. The cars
are placed in the kilns, which are long and tunnel-like insulated compartments where
they are subjected to controlled heat, humidity and air circulation.
After spending from ten days to two weeks in the kilns, the lumber is removed,
cooled gradually and is then reworked to remove defects; it is planed to thickness
and is then packed in bales for shipment via ocean steamer. On arrival in this country,
it is sold to other manufacturers, who cut the wood into the many useful things,
for which Balsa is so well suited.
Balsa (or balsawood, whichever you prefer to call it), has been the standard
material for model airframe construction since it first became available commercially
in suitable cut sizes some thirty-five years ago in this country and even earlier
in America. Although, botanically at least, balsa is only about the fourth or fifth
lightest wood in the world it is the first of all the woods which combine strength
with lightness. On a strength/weight basis, in fact, balsa compares favorably with
most other woods - even oak (see Table I). This is one of the main reasons why it
is so suitable for aeromodeling, where strength is required for minimum weight.
Many other materials which are as light as, or lighter than balsa, also fall down
on this question of combining strength with lightness and cannot be used in small
sections - expanded polystyrene, for example.
The other great advantage of balsa is the ease with which it can be cut or carved,
and joined with quick drying cement. Having a fairly open structure, balsa cement
impregnates and adheres strongly to balsa with the result that properly made glued
joints are as strong or stronger than the wood itself. With balsa readily available
in a wide range of sheet, strip and block sizes, very few tools are required for
working balsa either in solid form or for the assembly of built-up frames, etc.
At the same time, however, there are disadvantages. The balsa tree is very fast
growing, reaching a height of 15 feet of more within a year and growing to between
60 and 90 feet within the next six to ten years. After that time the tree begins
to deteriorate and rot. As a result both the density and quality of the lumber obtained
by felling balsa trees can vary enormously.
SIG - The Most Famous Name in Balsa!
Reprinted from Aero-Modeler
The actual density of balsa can vary from as little as 4 lb./cu. ft. to as much
as 24 lb./cu. ft. (which is about the same as obeche). Practically all the commercial
balsa available, however, falls within the range of 6 to 16 lb./cu. ft. with the
overall average tending to run about 9-10 lb./cu. ft. The strength properties of
balsa vary directly with density - the heavier the wood the stronger it is.
Balsa is normally graded by density, although, the actual descriptions are largely
arbitrary and not always identical between different suppliers, or different model
designers specifying grades to be used. The most general commercial classification
is "light", "medium" and "hard", as below -
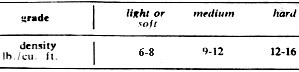
The more expert modelers adopt a wide. range of grading, typically as below -

Logically one selects the lightest grades for the lightly stressed parts (e.g.
block wing tips, sheet fill ins, etc.)and the heavier grades for spars and longerons.
Even here, however, practice can differ. Some modelers prefer to use very hard balsa
for longerons and spars and keep weight to minimum by reducing the actual size of
the sections used. Others prefer to use a lighter grade and compensate for strength
by using larger section.
Note: the strength/weight ratio of 10 lb. cu. ft. Balsa is rated at 100 and the
strength/weight ratios of other woods calculated accordingly. Thus a figure of less
than 100 shows a performance inferior to 10 lb balsa on a strength/weight basis;
and a figure of over 100 a superior performance
Both systems have there advantages and disadvantages. The use of hard grades
and small sections actually gives the best overall strength to weight ratio (see
Table I). On the other hand, the smaller size spars may be more difficult to handle
for building and also lack local stiffness. Using larger sizes normally gives greater
stiffness and local strength, although it is also easy to add excess weight as well
unless the grade is carefully selected. Also if too light a stock is chosen in the
interests of saving weight, the resulting structure may be weak. For most purposes,
however, Table II can be used as a guide for balsa grade selection.
In practice, grade selection can only be made with reference to actual weights
of individual sheets or strip lengths. To save having to work out density in each
case, consult Tables III, IV and V.
A tip to remember here is that as far as grading is concerned, suppliers of cut
balsa tend to favor selection of the harder grades for the smaller sizes (or thickness)
of strip and sheet as being easier to handle. Thus one is more likely to find mostly
"hard" grade in 1/16 in. sq. for example, and more medium to soft in 3/8 in. sq.
Similarly, the proportion of "soft" is likely to be higher in 3/8 in. and 1/4 in.
sheet than in 1/32 in. or 1/16 in. sheet.
In point of fact "cut" is more important than appearance in the case of sheet
stock since this largely controls the rigidity, or strength of the sheet. And cut
depends on the way the original lumber is cut from the log and then finally machined
- see Fig 1. If the "cut" is such that the annular rings effectively run across
the thickness of the sheet (tangent cut) the sheet will be fairly flexible, edge
to edge. It, on the other hand, the cut is such that the annular rings run across
the thickness of the sheet (radial or quarter-grain sawn), the sheet will be rigid.
It will also be appreciated that a piece of lumber cut from either section A or
section C of the log can have a final cut for turning into sheet which is either
tangent or quarter grain, depending on which face the cut is made from. If the section
of lumber is "random cut" the grain direction is less clearly defined and irrespective
of the direction of final cut the sheets will have intermediate properties between
"tangent cut" and "quarter-grain".
It is difficult to distinguish between random cut and tangent cut by appearance,
or even by simple bending tests, but quarter grain shows up quite clearly by the
speckled appearance of the surface. True quarter-grain sheet, in fact, would be
too stiff to bend to even moderate curvatures without splitting - and quite impossible
to roll into a tube shape as can be done with carefully selected light density tangent
cut stock.
Again "cut" recommendations are summarized in the form of a table for convenience
of reference (Table VI). The point to bear in mind is that "cut" and "grade" are
interrelated, so that the best choice of balsa for a particular job is based on
both. This applies particularly in the case of sheet balsa parts. The stiffness
or otherwise of spars is best judged by actual test - e.g. to obtain a pair of matched
spars, select two of equal weight and appearance .
In this manner, and in the latter case in particular this may mean examining
and testing a considerable number of individual strip lengths in order to arrive
at a set of four more or less identical pieces. Many experienced modellers, in fact,
prefer to cut longerons and spars from sheet stock in order to achieve complete
matching. In general, however, this is only advantageous where relatively small
sizes are involved - e.g. longerons not greater than 5/32 in. sq. section and spars
not more than 1/8 in. thick. Cut longerons and spars in thicker sheet generally
suffer from inaccuracies due to the difficulty of making long accurate "square"
cuts in thicker sheets.
In cutting a set of matched longerons, the sheet should be marked before cutting
(e.g. with a ball pen) so that the final lengths are identified end for end and
used the same way round for a complete match - Fig. 2. The same applies to cutting
parallel spars. In the case of tapered spars however, the best match is obtained
by cutting the two spars about a common "bottom" line rather than an angled cut
separating the two - see. Fig. 3.
A modeling blade with a fine taper is usually best for cutting fine sheet. The
same blade may also be used for parting off longeron and spacer sections up to 1/8
in. square; although some modelers find it easier to work with a less tapered blade
- Fig. 4. The squarer blade is also better for cutting thicker sheet as the fine
tapered blade can more readily run off "square". The razor saw comes into its own
for cutting larger sections.
The best direction of cut is normally obvious, but some specific recommendations
are. summarized in Fig. 5, together with explanatory notes. The main thing is to
avoid stressing balsa sheets across the grain (in which direction it is weakest),
so cross grain cuts should always be made from the edge inwards, rather than outwards
towards an edge. Also, when cutting at an acute angle to the grain, make the direction
of cut so that the grain will tend to pull the blade away from rather than into
the component shape.
Resources for Balsa Wood on the Airplanes and Rockets website:
|