Rubber-powered
free flight, to the uninitiated, might appear to be a simple sport.
Maybe even to the casual free flighter is simple. Wind the rubber band,
launch the model, recover the model, repeat. Truthfully, that's about
the way it has always been for me. However, many free flight enthusiasts
are more competitive and like to know how to get the most performance
out of every inch or ounce of rubber. As with most aspects of every
hobby, the science of rubber motors has become quite precise. Even as
far back as 1968, when this article appeared in American Aircraft Modeler,
hobbyists were experimenting with rubber dimensions, chemical composition,
elasticity, weight, tension, turns-per-inch, and every other conceivable
parameter available for measurement. Typically, experimentation begins
with observing and recording behavior of physical actions and reactions,
then a theory is derived from empirical testing. Equations are developed
that match measurements, and then more measurements are made under new
conditions to determine whether the derived formulas pertain to all
scenarios. If not, then new equations are derived to account for idiosyncrasies.
One of the most interesting findings, in my opinion, is that
it takes about 24 hours for a rubber motor to restore itself to full
strength after being wound. The main lesson from the story, however,
is that breaking in the rubber by stretching it rather than winding
it accomplishes the same result, but saves wear and tear on the rubber
by not needing to be twisted to break it in. Rubber Motor Testing
Jim Horton
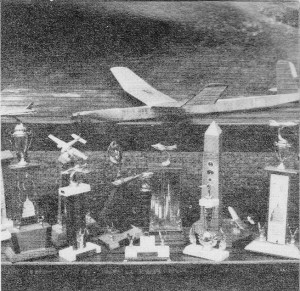
Unlimited design by Horton has enviable contest record of 11 trophies.
Motor test procedures described in articles were used on this model.
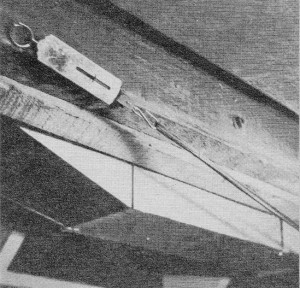
Rubber motors were stretched four times original length for a period
of 72 hours. Cool, dark basement was convenient. Light has an adverse
effect on rubber.
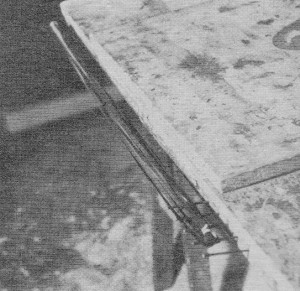
Motors were made up to required length around nails in workbench.
Additional nails at one inch intervals indicate perma-nent break-in
stretch.
AFTER getting poor and varying results with several pounds of Pirelli
rubber, we decided something was lacking in our technique. A simple
straight forward test was needed to determine the physical state of
a rubber motor. Such a procedure, useful while breaking in the motor,
would also indicate its contest-life capability and serve, too, as an
indicator of quality from one batch of rubber to the next. We
decided to measure the force, in pounds, developed by a motor stretched
to a fixed length. A simple spring scale measuring from zero to 50 pounds
was purchased at a hardware store. Our Unlimited design motor, 18 strands
of 1/4" x 1/24" Pirelli 32 in. long, was stretched to three times its
original length, and readings were taken on the spring scale.
Throughout the contest season readings were taken not only after
motor break-in but also after each contest flown with four of the motors.
Chart 1 gives the force profile of these motors. Standard, conventional
break-in procedure was used -- motors were stretch wound, increasing
the turn count by 10% each time until the maximum turns-per-inch (18
in our case) was reached. Our results, as indicated on the chart, show
that after a motor is completely broken in, the force line becomes constant.
Armed with these readings we decided that, if motors could be
broken in without winding, their useful life could be extended. To reduce
erratic results a controlled stretch method was used. Motors were stretched
four times their original length and readings taken with the scale at
24-hour intervals. We were amazed to find that it took three days to
break in a motor. At the end of this period, "controlled-stretch" motors
were giving the same tension force readings as those obtained from broken-in
motors of the previous contest season. Permanent stretch was also the
same -- motors increased their length three inches, from 32 to 35, after
break-in. These motors have been used in two contests this past
season and wound to 18 turns per inch on each flight. So far we have
not broken a single strand and the force readings have remained constant.
Chart 2 gives the force profile of the motors used. Some interesting
byproducts resulted from this testing. At one meet last season, we had
a real dud of a flight after making two. maxes. Naturally, we were ready
to place the blame on a dead motor. A quick check with the scale indicated,
however, that the motor was in perfect shape, shooting down another
good excuse. Another interesting point was noted: it takes the motors
24 hours to fully recover from a winding to maximum turns. Readings
taken immediately after full contest turns will not be the same as 24
hours later. All chart readings given here were made after this rest
period in order to keep results consistent. It's amazing how strong
the motors were; even after a season's flying, they registered the same
tension force readings. In fact, motors were retired due to age rather
than weakness. Strands popped, causing an excess of knots. One
strong message was clearly given on the force charts. Motors cannot
be wound to a contest turns maximum without proper break-in. Fresh Pirelli
will develop high stresses and has been known to blow at 50% of normal
turn capacity. Remember, this article is specifically for the
motors we used. However, this procedure can be used to evaluate any
size or length of motor. We feel these tests useful for the contest
flyer.
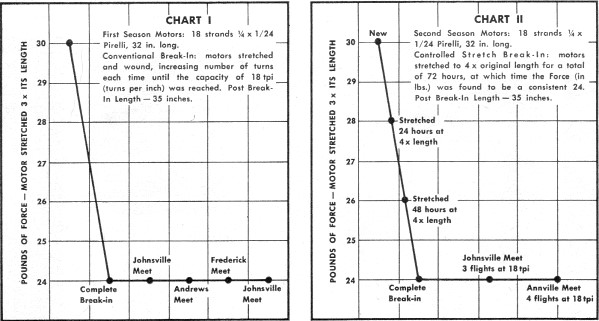 Charts compare both conventional
and controlled-stretch break-in procedures over two seasons of competition.
Force readings and amount of stretch were the same for each.
Note: I'm not sure what
the horizontal axis represents, other than events in time, but then
why is the Johnsonville Meet (chart II) offset from the center of
the grid?
Articles About Engines and Motors for Model Airplanes, Boats, and Cars:
Posted
July 10, 2011
|