As with most of the handyman's
type of magazine of the era, Popular Science features a very broad array
of topics, including full size and model aeroplanes. The May 1968 issue of
Popular Mechanics had plans
for a full-size
homebuilt airplane made of spruce and plywood, using a modified
Volkswagen engine. This June 1941 issue had plans for building a rubber powered
free flight model dubbed the "Minute Man." It is a simple stick and tissue job that
can be built for a few pennies worth (at the time) of balsa, glue, Jap tissue, and
rubber (of course in today's hyperinflated Bidenomics world the price is measured
in dollars). Old timers like myself are familiar with the designer,
Frank
Zaic. He was the founder of the Academy of Model Aeronautics (AMA) in 1936,
an organization which still thrives today. He was also co-founder of
Model Aviation magazine, which
has undergone a myriad of name changes over the years, and is now back to it's original
name. Frank's experience as a draftsman for the U.S. Patent Office is apparent in
the quality of his plans, as can be seen below.
All-Balsa Plane Model ... The Minute Man
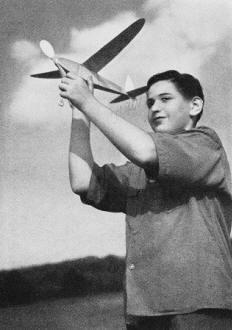
All materials for this trim little ship cost less than half a
dollar.
By Frank Zaic
Editor of the "Model Aeronautics Year Book."
This little plane, capable of flights of over 2,000 feet, can be built and launched
in less time than is usually required to construct the fuselage of more complicated
models. Its sturdy, simple design is an instructive example of what can be done
with lightweight and quarter-grained ("C" cut) balsa sheets (see P.S.M., Dec. '40,
p. 198).
In selecting the balsa, see that it is light and shows the speckled surface which
identifies "C" grain. Cut the fuselage and wing parts cleanly with a sharp blade
to produce smooth edges. The dimensions of the fuselage cross braces should be taken
from the numbered scale which appears in the drawings. Notice, in the detail of
the nose, how the eight braces are offset for maximum strength. Spread cement carefully
along the full length of the edges when assembling the fuselage. The top and bottom
sheets are trimmed flush with the sides after the cement has hardened.
The wing camber is obtained by moistening the under surface with water, and allowing
the single end rib to extend the camber along each wing. The sheet may at first
tend to curve upward, but will assume the proper downward curve as it dries. When
it is quite dry, apply broad streaks of cement to the underside, as shown in the
drawings. These are important.
Cut the propeller blank from a straight-grained block of balsa, 7/8" by 1 7/8"
by 8".
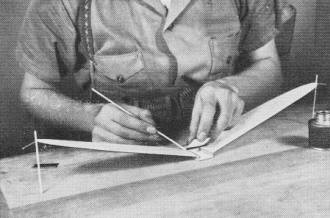
Form the dihedral angle by elevating wing tips three inches above
the center, and cement on the overlapping strip and fairing block.
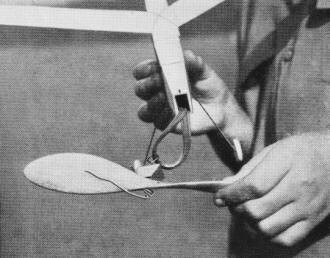
Propeller, detachable nose block, "freewheeler," and rubber motor.
The hook on the propeller engages the shaft while motor is under tension, springing
free when the energy of the rubber is exhausted.
Because no model plane is better than its propeller, the builder is urged to
read the instructions given in the article following this one.
The freewheeling device shown in the plans operates in this way: The long hook
is so fastened to the propeller that it normally springs out of contact with the
triangular hook on the motor shaft. After the rubber is wound, the hooks are engaged
by hand. When the motor has been exhausted in flight, the propeller overruns the
shaft, and the long hook springs free, permitting the propeller to turn upon the
shaft. It is important that there be no friction between propeller and shaft once
the hooks are disengaged. A drag at this point may cause the propeller to act as
a rudder during the glide, spoiling the model's performance. In the case of a small
ship such as this, a dragging propeller may even cause it to spin down in a spiral
dive when the rubber is exhausted.
The motor consists of six strands of 1/8" flat rubber. Form it by winding the
rubber over two nails placed 15" apart. Wet the ends, and tie with several knots.
Lubricate the motor with glycerin before pulling it through the fuselage.
The nose block is made of two parts cemented together, its upper face being grooved
for the rubber band which holds it to the fuselage. An eyelet is used for the shaft
bearing. The fuselage shape shown will give the nose block an offset or down thrust
of 1/16". After test flights have been made, or when the motor is to be wound up
for maximum duration (700 turns), the nose block should be given about 1/16" right
thrust. Only experiment will determine exactly the correct amount.
Before flying it under power, test the model's glide. Move the wing back if the
ship stalls, or forward if it tends to dive. The rudder may be warped if a circular
flight is desired. After a smooth, flat glide is obtained, make a test flight with
the motor partly wound, and correct the wing setting if necessary. Once the adjustments
have been made, the ship should readily make flights of more than a minute's duration
in calm air.
Simplicity and sturdiness¢ are the keynotes of this all-balsa design. Study the
plans before starting work.
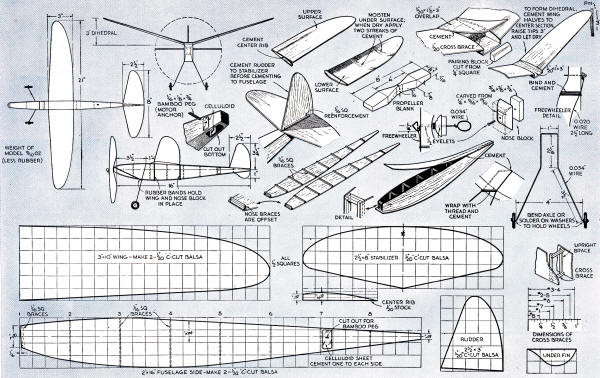
Minute Man Plans
List of Materials
2 pc. "C" cut balsa 1/32" by 2" by 36" for fuselage
1 pc. "C" cut balsa 1/20" by 3" by 36" for wing and tail
2 pc. hard balsa 1/16" square by 36" for fuselage braces
1 pc. balsa 7/8" by 1 1/8" by 8" for propeller
1 pc. balsa1/4" by 1" by 2" for nose block and fairing block
1 pc. 0.034" piano wire, 24" long, for landing gear
1 pc. 0.020" piano wire, 3" long, for freewheeler
8' rubber strand, 1/8" flat (brown); 1 pair hardwood wheels, 1" diameter; 4 washers,
3/16"; 2 shaft bushings, 1/2'' long; cement, celluloid, bamboo, rubber bands.
Estimated cost: about 35 cents.
Posted September 30, 2023
|