It is a dream job that very few aircraft modelers
ever had the opportunity to hold - working in the model shop of an airplane manufacturer crating scaled-down
versions of full-scale aircraft for use in proof of concept testing. Back in the days preceding sophisticated
computer aided design software, slide rules, tables of values, nomographs, rules of thumb, and wind
tunnels are all that were available to engineers when creating and testing new aircraft designs of modifications
to existing airplanes. A high degree of precision in the models was needed to be useful during the design
and manufacturing of production planes. Whereas with a computer a relatively simple change might take
only minutes to incorporate and re-analyze, a hand-built physical model could take days or weeks to
modify and re-test in a wind or smoke tunnel. I am amazed that so much progress was made given the crude
tools available at the time, and I'm equally amazed at the rapid advancement in aerodynamics and powerplants
available from today's designers. Most, if not all, modern aircraft designs still go through some level
of scale modeling prior to building the first full-scale prototype, so these jobs do exist even now.
Snagging one of them, though, is as unlikely as it was half a century ago.
Modeling for Money
Out in a secluded corner of the big Chance Vought aircraft plant in Dallas, Texas, is a group of
men who get paid for doing what they enjoy most-making model airplanes. These are not models that fly,
but ones that are used for wind tunnel testing of the big jets which CVA makes for the Navy, such as
the F7U-3 Cutlass, the guided missile Regulus and the XF8U-1 day fighter. Other models are used for
exhibition and sales promotion purposes. Half the men still build and fly in meets.
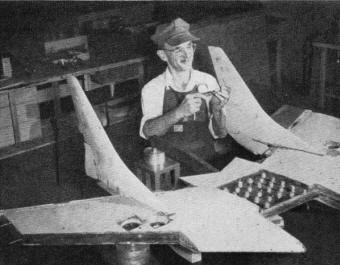
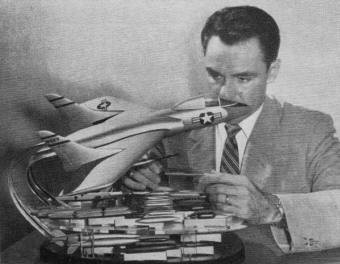
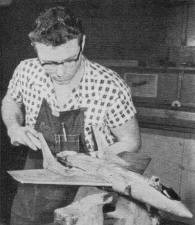
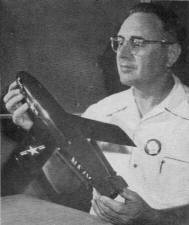
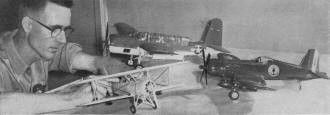
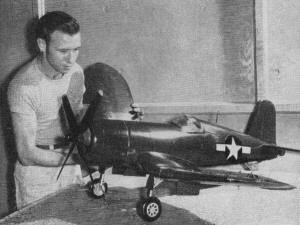
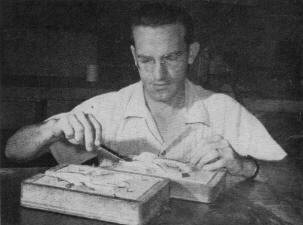
Posted April 26, 2014
|