As with most electrical and electronic
equipment, performance increases have come often and significantly in the six
and a half decades
wince the article was written. In 1957 when this article appeared in
American Modeler magazine, battery technology was still crude by today's
standards, but much advancement had been accomplished during the war years of WWII
and Korea for the sake of field portable communications gear. Chemistry and packaging
improved to where if the user was knowledgeable and applied certain precautions,
a high degree of reliability could be garnered from various cell types. Having the
right battery for the task at hand was and still is paramount to achieving success.
It is interesting that vibrator type DC-to-AC power supplies (e.g., the
Mallory Vibrapack)
were still being used to supply the high plate voltage for electron tubes. Some higher
voltage batteries could be connected in series instead, but that often resulted
in too heavy and too bulky packs that could not be readily accommodated by the airplane
model.
Battery problems spoiling your R/C fun? Then heed these words
of wisdom from Worth!
There appears to be a widespread lack of
knowledge concerning the care, maintenance and economical use of batteries for radio
control modeling purposes. Those who complain of short battery life and undependable
performance seem to greatly outnumber those who have overcome these problems by
learning the "know-how" of successful battery handling. Presented here are many
of these details with the hope that reliable and efficient use of batteries may
be promoted on a larger scale.
Selecting Batteries. Sizes must be chosen which are adequate
for the current drain involved. This factor is frequently compromised where minimum
weight is required, with the result that batteries are used which are too small
for reliable operation of the equipment. Weight saving in this manner breeds complaints.
Yet it is often possible to utilize other equipment, even if somewhat heavier, to
gain an overall weight savings if resulting current drain is low enough to permit
reducing battery weight.
Big savings are possible in this manner in filament and actuator circuits. Subminiature
tubes with low "A" battery drain offer considerable space and weight savings over
their 7 pin (miniature tube) big brothers with little performance sacrifice. Also,
some d.c. motors used for actuators have far less drain than others with no penalty
in power loss, but with substantial reduction in battery weight required.
Selecting batteries, therefore, is very closely tied in with the equipment requirements.
Current drain reduction is thus the key to battery weight reduction for once the
current drain is determined battery selection narrows down.
Table I indicates current drain limits for batteries with performances proved
in practice, though it should be kept in mind that there are other factors to consider.
For instance, higher drains can be tolerated if they are intermittent. Escapements
with current drains as much as 50% higher than those shown can be used with a particular
battery since they are seldom energized for more than a few seconds at a time. Likewise,
pulsing actuators average out an operating drain of about half their full stall
figure. It is on this average operating drain that the table is based.
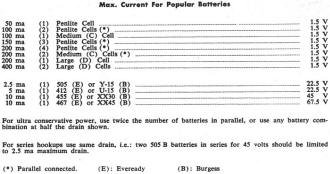
Table I - Maximum Current For Popular Batteries
Flight durations of only 2 to 3 minutes can tolerate drains about 1/4 higher
than those shown since the table is about right for plane flights in the 5 to 10
minute range to provide at least a day's flying without concern. However, where
higher drains are involved, operating times should be followed by rest periods 4
or 5 times as long.
Remember the temperature factor, too. For near or below freezing, double up on
battery size to make up for the reduced capacity that cold causes (explained later).
Only the most popular batteries are listed. Experience shows that odd sizes are
hard to find in fresh condition, since they are less in demand. This brings up the
next important consideration:
Purchasing Batteries. I disregard brand names. Competition in
the battery field is fierce and differences between brands is less a factor than
the matter of freshness. Batteries will gradually deteriorate, even if not used,
due to an internal self-discharge process. This is more important to small batteries
than large, since a little loss of capacity involves a bigger percentage of useful
life. Reliable use of small batteries is directly related to freshness.
Don't expect much from the dating used on some batteries. Dates less than three
months ahead are helpful to warn of stale batteries, but with dates farther ahead
there is no sure indication of freshness and usually it is more important to consider
the conditions under which the battery has been sitting on the shelf. Particularly
during the summer, battery freshness can be seriously affected by storage conditions.
From this viewpoint, a battery which has been stored in a shaded area of an air-conditioned
store is more likely to be in better shape than one which has been displayed in
a hot window exposed to the sun.
"Turnover" is the big consideration when you're nosing around for a source of
fresh batteries. Rapid turnover means frequent reordering and it is important because
it reduces the time between the manufacture of a battery and its purchase so that
much of the battery's life is not wasted while it's on a shelf.
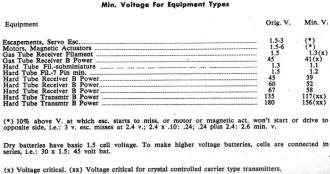
Table II - Minimum Voltage For Equipment Types
It may be the local drugstore, radio shop, Sears or Ward outlet, or some other
store that replaces its stock most often. Note: a good source in one locality does
not always indicate a similar good source elsewhere. Be wary of large stocks per
se as they could indicate long periods between restocking. A better indication is
a small selection of popular sizes which is observed to be replenished frequently.
Testing before buying is often possible. An on-the-ball dealer will test for
you and this in itself indicates that he probably is a good battery source. Usually,
the only test a dealer will permit is a no-load voltage check, but this is helpful
to eliminate the obviously bad batteries. A battery should read at least the voltage
printed on it. Really fresh batteries will usually indicate slightly more.
Store checks can be a great education to both dealer and buyer. Both often discover
that many supposedly brand new batteries have pooped out somewhere along the line.
A dealer thus educated is likely to become a good battery source shortly afterward
since he then is a more demanding purchaser himself.
Testing Batteries. Voltage checks, the primary key to battery
condition, are accurate only when made under load. A check under load means that
the circuit for the battery is operating and drawing its normal maximum current.
An equivalent load can be provided by means of a resistance that will indicate similarly.
A load check procedure is usually obvious, but not always. In most cases, you
simply switch on the circuit, connect the meter across the batteries for that circuit
and read the voltage. But in a Lorenz two-stage receiver, for example, just switching
on the circuit does not result in maximum B current drain. The 2nd stage must be
triggered by keying the transmitter or by cutting off the 1st tube current. Then
the B voltage check will be a true indication since much more current is drawn by
the 2nd stage than the 1st, even after subtracting the drop in the 1st stage when
keyed.
On the other hand, for a filament voltage check it makes no difference what the
B current is.
In load checking, you must understand that there are different acceptable minimum
operating voltages for various types of equipment. Experience suggests the values
shown in Table II.
Circuits considered voltage critical require fresh batteries for reliable operation.
However, these batteries need not be discarded after removal from such circuits;
they may be used for less critical purposes. In checking circuit under load, consider
1.1 volts per cell to be the end of a dry battery's useful life. Batteries use up
roughly 1/3 their life dropping from 1.5 to 1.3 volts and the other 2/3 down to
1.1 volts. Therefore, equipment which will operate reliably down to 1.2 basic cell
voltage offers maximum battery economy and freedom from constant voltage checking.
B batteries should be checked only for voltage. While "A" batteries can stand
a maximum current check for better indication of capacity, this is not recommended
for new A's since it can ruin them if not done properly. Also, above 1.3 a load
voltage check gives a good enough indication of battery condition. But between 1.3
and 1.2 volts the capacity remaining in a battery is more doubtful. Since the battery
is already on the way out, a current check can't cause too great a loss and it can
help select those which have greatest capacity left. An Ammeter (not a milliammeter)
with a scale of about 5 or 10 amperes is needed.
With the battery not connected to any circuit, connect the meter momentarily
directly across the battery terminals and note the maximum reading. The meter must
not be connected for more than the briefest interval it takes to get a definite
reading! Make sure polarity is right: Plus to plus. A usable battery will indicate
1 ampere but this is okay only for lowest drain circuits. At least 1.5 amps is fair;
anything over 2 is good.
Operating Practices. The so-called dry cell charger is very
practical for keeping good B batteries in top shape. This charger merely depolarizes
a battery, which means it breaks down a chemical accumulation that builds up in
a battery to prevent all of its energy from being used. Regular and proper use of
a charger has maintained hearing-aid batteries in use for over 2 years, as compared
with their normal life of about 6 months. But a charger will not restore an excessively
rundown battery to reliable use. Also, the. gain from charging A batteries is much
less, for the handling involved, so do not expect too much from a charger other
than as described.
Reasonable care is needed at home and on the field to get the most out of batteries.
Avoid excessive overheating, such as results when you leave a battery in the trunk
of a summer sun baked car, or in an uninsulated attic. Same goes for a model or
transmitter left out under a broiling sun to cook for several hours while you wait
for the wind to die down. A light colored cloth thrown over the top is a help, but
putting the gear under the car is better.
Keeping batteries near (not inside) an ice cooler is good, too. Refrigerator
storage of good batteries, particularly hearing-aids, is helpful between hot weather
flying sessions or long periods of inactivity. But care must be taken to avoid freezing
and to keep the batteries dry. Cold slows down the chemical action in a battery
and minimizes the self-discharge process. To restore the batteries, allow several
hours of thawing, followed by 15 to 20 minutes charging.
Because extreme cold slows down the chemical action of a battery it also effectively
reduces its capacity since it lessens the production of electrical energy. Hearing-aid
batteries suffer most in cold weather since their cells are already very small.
Even D cells may be only the equivalent of pen cells in extreme cold. Unless your
battery supply is extra conservative, keep cold weather flights under five minutes
and swap batteries regularly. Keep a spare set warm in an inside pocket between
flights (it doesn't help much to swap with cold batteries from the tool kit).
The small portable radio type batteries (XX45, 467, etc.) used commonly for transmitters
are made up of stacks which basically are double-size hearing aid cells assembled
in groups to provide high voltage in a convenient package. Capacity for high drains
therefore is not great. Far more transmitter reliability may be had with larger
heavy-duty or industrial sizes which are made up of at least pencell stacks. This
is most important for carrier wave crystal controlled transmitters since their output
falls sharply with decreased B voltage.
Use of Vibrapack or dynamotor power is fast becoming standard for transmitter
operation because large batteries are costly and current drains are high. These
power units use a basic heavy duty wet cell supply which eliminates the need for
dry batteries in the transmitter.
Despite the high initial investment required for this type power unit, which
must include a charger for the wet cell (unless a car battery is utilized), the
cost in the long run is less. The Vibrapack power supply, popularized in the famed
Mac II transmitter, increases the reliability of ground R/C equipment so greatly
that it is no longer considered a problem. Some Mac II's have been going for over
five years with the same 2 volt wet cell and give no indication of quitting! More
importantly, transmitter operation has never been in doubt. This alone justifies
the investment.
But don't assume that wet cells are a cure-all for every power problem. The large
types used for transmitters are relatively simple to handle, but the miniature wet
cells have more charging and maintenance headaches which tend to discourage their
use except for special requirements. For other than heaviest duty applications,
dry cells have proved to be economical and reliable, if properly used.
It is the long run cost that can make or break the economy of any battery problem.
On this basis, the extra life gained from the use of larger batteries usually makes
up for their higher initial price. On the same basis, the use of wet cells, chargers,
special power supplies, etc., need not be rough on the wallet, But no matter what
the cost, there is no economy without reliability.
Posted March 30, 2022 (updated from original post on 11/26/2016)
|