Here is a nice free flight rubber
model for builders of average skill. The Curfew appeared in the September 1973 edition
of American Aircraft Modeler. In order to help make this and other difficult to find
material available to everyone, I have scanned the original article from my purchased
copy. The text has been OCRed to make it searchable. AMA might still sell the plans for
the Curlew (see bottom of page for scanned version).
Curlew
A most handsome and stylish rubber model adaptable to Coupe but really intended for sport
flying. Duration - about two minutes in dead air.by George Brownfield
Fred Bodsworth of Toronto, Canada, has written
a book called Last of the Curlews, a classic. The Curlew, which winters on the Antarctic
tip of South America and flies almost halfway around the world to breed in the Arctic
Circle, has probably become extinct. My model, the Curlew, is a tribute to the stamina
and courage of one of the world's most beautiful creatures.
Construction
Fuselage: Trace one side carefully on a 1/32" medium quarter grain sheet
using a sharp, medium hard pencil and carbon paper. Cut a second sheet the same length
and stack them together with a small piece of masking tape on each end so they will not
slip when you cut through both sheets. Now cut out the sides going slowly around the
little radius on the back window. Both sides will be identical using this method. Pin
the sides down over the plans and glue in the cabin struts and the front window frame.
After cabin struts are dry on both halves, trace the 1/16" stiffeners on the inside
of each fuselage half, being careful not to press too hard. Glue the longerons on first
by rolling them lightly with a dowel or a round pencil. The 1/16" square stringers will
nearly take on the same curve of the body and simplify gluing them in place. Cut each
stiffener and glue in place. Don't forget the landing gear angle pieces, which should
be glued well.
Joining the two fuselage halves isn't difficult, but it does take a little patience
and care to insure proper alignment. Prop the sides upright on your work board and glue
in the front dihedral cross brace and the bottom cross brace. Join the fuselage ends
at the back with the cross members directly behind the aluminum rubber holding tube.
Check that the sides are drying squarely with no twist built into the fuselage. When
thoroughly dry, the rest of the cross braces are quite easy to install. Bring the nose
together with its cross members in place and hold with a strip of masking tape. Make
sure the members have no crooked pieces and double glue for extra strength. Set the fuselage
aside to dry and proceed to build the rear part of the fuselage directly over the plans.
Build both halves with 1/16" square balsa. When dry, butt the two pieces up against the
main fuselage and glue the tips together. Set the fuselage on the top view of the plans
to make certain the back two rear fuselage halves dry in line with the cabin section.
Add cross members seeing that nothing dries out of line. When the whole body is dry,
lightly sand all joints to eliminate any bumps of glue. Bend the landing gear out of
1/32" music wire and sandwich it in place with the pieces shown in the small diagram.
Ready for maiden flight. Her sporty paint scheme
is really just colored tissue. Note the rear motor peg is aluminum tube which also serves
as the dethermalizer fuse's snuffer tube.
When dry, glue the whole assembly in the fuselage. This area should be securely plastered
with glue. After the gear is dry, proceed with the planking of the top and bottom of
the cabin section as shown in the small illustrations. Construct the wheel pants and
sand a radius on the outer edge. When both have identical shapes, glue the plywood oval
disk on the side of the wheel pant which butts up against the wire landing gear. Slip
the wheel inside the wheel cover and install the assembly on the axle, making sure the
oval plywood rests up against the landing gear. Mix up a small batch of epoxy and secure
the wheel pant to the landing gear with the wheel installed. Set the fuselage on your
work board with the wheel pants propped up at the right until the epoxy cures. The landing
gear fairings are made from 1/16" sheet and glued to the inside of the wheel pant.
Wing and Stabilizer: Cut all ribs from 1/32" quarter grain wood. Rub a bar of
soap or a white candle on your plans where all glue joints will be made to prevent the
structure from sticking to the plans. Pin down the leading edge and trailing edge on
the wing, and the leading, trailing edges and the 1/16 x 1/8" spar on the stabilizer.
The trailing edge of the wing will have to be shimmed up with small pieces of balsa to
allow the ribs to enter the notches in the trailing edge at the right angle. (See plans
for detail.) For the ribs on the tip of the wing, cut to proper length and sand the oversize
areas away after the wing has been removed from your work board.
Glue spars in now! Note that the dotted-line ribs are left out until the dihedral
gussets have been installed inside the leading edge and spars. When the dihedral has
dried in he wing, cut the standard rib to fit in he dihedral break areas and glue them
in place. Be sure the center dihedral break has been glued well! The stabilizer has two
different size ribs. Be careful to put the longer rib in as the angle brace and the shorter
one in as the conventional rib. This helps to discourage warping in the stabilizer. When
both wing and stabilizer are dry, sand carefully to the airfoil shape shown on the plans.
Propeller: Making a successful folding propeller may seem complicated at
first, but if the steps are followed, you should turn out a fairly high performance rubber
folding propeller. The success you have in this particular area of construction will
make a big difference in the performance of your Curlew, so take your time in carving
the propeller block. Use a sharp knife and sandpaper -and don't hurry!
A standard block this size can be purchased at any hobby shop in a 12-in. length.
Cut off the extra three in. and very accurately trace the dimensions on the face and
sides of the block. A hacksaw blade makes an excellent tool with which to cut out the
block. Start carving the front of the propeller from the leading edge down to the trailing
edge of the block. (Check drawing and you will see what I mean.) Carving is actually
fun, but you must be careful not to slice out too large a piece. Whittle away small pieces
rather than hacking out big ones.
Watch the grain of the propeller as you carve away the balsa. It will be necessary
to turn the propeller blank around and carve in the opposite direction many times because
the grain of the balsa changes as you carve the shape of the blade. The partially finished
blade in step No.2 should have an airfoil shape similar to the cross section drawing
in the propeller blade template.
That's all there is to it! Now it's time for
tissuing. Wing is not a complicated, warp-proof structure, so use thinned dope sparingly.
After you have carved the propeller to look like step No.2, position the finished
blade template on the front of the blades and trace around the template. Cut away the
excess balsa and re-sand the blades to their final shape as shown in step No.3. The front
and back bearing plates are made from a tin can or thin brass strips 1/64" thick. Drill
.046 holes in the front bearing plate and the one hole in the back bearing plate. 1/16"
00 aluminum tubing 1/4" long is attached with epoxy in the area shown in step NO.4. Slip
a straight .046 wire through the propeller hole and install the front and back bearing
plates. Bind with thread or gauze and glue. The hinge wires are 1/32" music wire 21f4"
long: Slip wires through the little tubes and bend one end to fit on the front surface
of the propeller blade and the other end on the back side of the-blade. Two needle-nose
pliers are best suited for this task. This step is probably the most difficult part of
building your folding propeller, so don't get discouraged. After you bend both wires
to lie as flat as possible on both blades, bind tightly with thread or use gauze and
epoxy the wires to the blades. Step No.5 shows how to bend the propeller shaft with a
pair of needle-nose pliers.
She's even equipped with a dethermalizer. The
glide is excellent. (Plans show complete folding prop assembly which is essential for
a good glide.)
After completing 5-F, slide shaft through the propeller hole and into the other hole
on the front of propeller hub. Now bind the shaft to the propeller hub and glue well.
When dry, slide on the spring, ball bearing washer (or small washers if a ball bearing
washer won't fit the nose block) and bend as shown in sketch No.6-A. Complete other bends
to Step E. Step E shows the extra wire cut off.
This little stub end of the wire should not scrape against the inside of the fuselage
when the propeller is turned. Slip a piece of neoprene tubing. or 1/8" gas line tubing
over this hook area to protect the rubber motor when wound tightly. Now it is time to
cut the blades so they will fold back. Use an X-acto saw or a fine hacksaw blade and
cut through the hub directly opposite the hinge tubes. The blades should fold back with
no binding. If there is a sticking or stiffness when they fold, put a drop of oil in
the little tube and work the blade back and forth until they fold easily along side the
fuselage. Insert the nose block and fold one blade on one side of the fuselage and the
other on the opposite side, as flush with the sides as possible. The spring at this point
should not be compressed but in its normal position.
When you have the blades where you would like them to fold, extract the propeller
and nose block without Changing its position. Mark a pencil dot directly to the right
of the stub end of the hook on the back of the nose block. This is where a 5/8" wood
screw will be inserted. This screw should be close enough to hit the stub end of the
propeller shaft and prevent it from turning. When the rubber motor is fully wound the
spring allows the prop shaft to clear the stop screw allowing the motor to unwind. As
the motor runs down, the spring gradually pushes the prop forward where the stub end
engages the wood screw and stops the prop exactly where you want it to fold. This may
take some adjustment, but the rubber motor should have a few winds left in it when the
propeller shaft hits the stop screw. The partially wound motor accomplishes three important
tasks: it keeps the balance of the Curlew constant, prevents the nose block from dropping
out, and stops the propeller just where you want it to fold. Give prop and nose block
three coats of dope.
Covering: Put a thin coat of clear butyrate dope on the sheeted part of the
fuselage using your favorite Japanese tissue color combination. Dope the tissue directly
to the sheeted area and shrink the tissue on the open structure. Give the whole body
one more clear coat of butyrate.
The propeller-assembled
and partially assembled.
Attach clear acetate windows after the body is covered and doped. The 1/16" dowels
which guide the braided nylon and the wooden bead at the back can be glued in place.
Pre-dope the wing on the leading edge, trailing edge and each rib on the undercambered
side only. Cover the bottom first in sections, securing the tissue to each cambered rib.
Remember, the grain of the tissue should run span-wise or wrinkles will occur. Cover
the top in sections also, but don't glue the tissue to the ribs. Spray the wing with
water and hold while it dries to prevent warping. When drum tight, give the wing two
thin coats of clear dope. Cover the stabilizer as you did the wing, but don't put dope
on the ribs. The tissue on the rudder will be tightened and doped once. Keep the tail
surfaces light.
Flying
The test model flew nicely on six strands of 1/8" Pirelli rubber. Four strands of
1/4" brown rubber also work fine. Add two strands at a time if more power is definitely
needed.
Balance the model as shown on the plans. If the Curlew is slightly tail heavy, slide
the wing back just a little. If model is still tail heavy, add coats of dope to the propeller
until proper balance is achieved. Bend the small tab on the rudder for a gentle right
turn.
Test fly the model on a quiet day over a tall grassy area. Launch the Curlew parallel
to the ground with a slight nose-down attitude. The glide should be a flat descent turning
gently to the right. Don't bend the rudder tab too far or a spiral dive may occur while
the model is under power. If the Curlew continually stalls in the glide, it still isn't
balanced properly or the stabilizer trailing edge isn't down tightly against the fuselage.
Be sure the fuse rubber band is strong enough to hold the trailing edge firmly against
the fuselage. If the model dives in the glide with the wing set according to the plans,
shim the wing up under the leading edge. Test glide the Curlew several times to make
sure the proper glide angle is achieved.
To wind the model, use a little inexpensive hand drill with a screw hook in the chuck.
Put the threaded end in the chuck as tightly as you can! Make sure the square knot in
the rubber motor is tight and the motor well lubricated. Have your partner hold the Curlew
firmly while you hook the propeller assembly and stretch out the rubber motor four to
six ft. Now wind clockwise about 30 turns on the drill while moving toward the nose of
the Curlew. Slip the nose block back into the Curlew while holding the hub of the propeller.
Gently launch the model parallel to the ground, releasing the propeller first then
the model. The model should climb steadily and in a right turn. Under no circumstances
should you let the Curlew climb to the left during the power run. If the model climbs
and stalls, insert down thrust by peeling thin layers from paper safety matches and gluing
them to the top of the nose block.
If the model climbs successfully but too straight, bend the rudder tab to the right
a little more. The best combination is a nice climbing right spiral. If the model glides
in a nice right circle, but still climbs straight out under power, add a bit of right
thrust. Shim the nose block the same as you did for down thrust by gluing a sliver of
paper on the left side of the nose block. Don't put in too much right thrust because
you al-ready have a right circle adjustment. There should be just enough to turn the
Curlew to the right during its climb . Too much right thrust causes a spiral dive which
could end up damaging your new model. The Curlew should climb nicely to the right, neither
stalling nor spiraling too steeply. Gradually increase the number of turns on the winder
to around 80. Check to make sure the hook in the winder will not slip out! Make necessary
thrust adjustments as you increase the winds. Don't exceed 350 turns on the motor, as
the motor will break if wound too tightly. Keep motor clean!
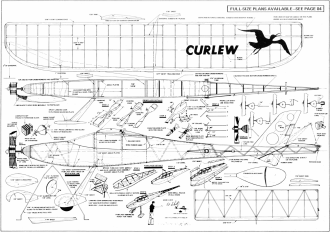
<click for larger version>
Notice:
The AMA Plans Service offers a
full-size version of many of the plans show here at a very reasonable cost. They
will scale the plans any size for you. It is always best to buy printed plans because
my scanner versions often have distortions that can cause parts to fit poorly. Purchasing
plans also help to support the operation of the
Academy of Model Aeronautics - the #1
advocate for model aviation throughout the world. If the AMA no longer has this
plan on file, I will be glad to send you my higher resolution version.
Try my Scale Calculator for
Model Airplane Plans.
Posted November 12, 2010
|