Here is an interesting concept in model wing construction
that probably would have become very popular in the prefabricated model market if the foam wing had
not been invented. Honeycomb has a very high strength-to-weight ratio when a compression force is applied
parallel to the cell height. When sandwiched between balsa (or maybe even cardboard) upper and lower
wing 'skins,' author Shepherd has found the scheme to be very satisfactory for all kinds of models.
BTW, words such as 'aluminium,' 'aerofoil,' 'centre,' etc., are not misspellings to the folks on the
other side of the pond. Oh, and a 'stone' as used here is a unit of weight (1 stone = 14 pounds), not
a physical rock ;-)
Honeycomb
Fantastic Strength in this New Type of Wing Structure
- By P. A. Shepherd
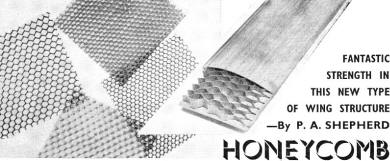
Are you seeking a method of constructing wings that is cheap, very strong and quick? These last three
things are not usually closely associated, but it is hoped to show that this is possible in the following
method. Wings described are especially suitable for radio models, large gliders, and control-line types.
In the full-size aircraft industry the same principle is known as double skin honeycomb construction
and is used for floors, doors and other components. With a core in aluminium foil, honeycomb structures
form much of the Vickers Vanguard control surfaces. Basis of the model version is 009 in. Kraft paper
honeycomb manufactured by Dufaylite Developments Ltd., of Boreham Wood, Herts. It is available in thicknesses
ranging from a quarter of an inch to six inches and with hexagons from three-eighths to 1 1/2 in. wide
in sheets measuring 36 x 12 in. (expanded). These compress to 1 in. x 1 in. x 18 in. rather like a paper
garland, it also expands like a paper garland and whilst it is compressed the required aerofoil profile
may be drawn on the end and the "block" sanded to shape (Fig. 1).
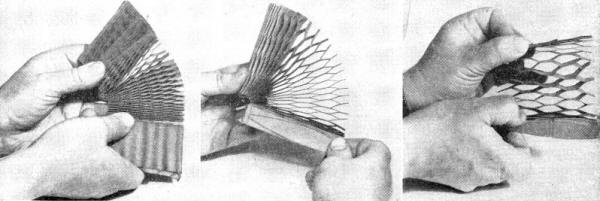
Heading shows rigid "Dufaylite Honeycomb" in impregnated materials" and inset. Mr.
Shepherd's test sample which we can assure readers, will stand up to a car running over it, or a 16-stone
heavyweight tramping on it! Below, a block of "Dufaylite Honeycomb" centre; with symmetrical rib marked
on face for shaping, and at right, shaped for covering with sheet.
Next stage in construction is to expand the honeycomb so that the hexagonal cells are approximately
equal in size. It should be noted that during this operation the material contracts by one-third in
a chordwise direction and due allowance should be made for this. The brown paper core should then be
pinned to the building board in the stretched state.
Next
job is to apply the upper and lower skins. 1/32 in. thick balsa should suffice for most wings up to
about 48 in. span or in certain cases up to as much as six feet. Since balsa is normally obtainable
in 4 in. wide sheets, as the maximum, wings of greater chord than 4 in. should have a stringer of about
1/8 in. x 1/32 in. balsa let in flush with the surface to enable two balsa sheets or more as required
to be joined to give maximum strength (Fig. 2). The skins can then be glued in place and pinned to the
board until dry. Best adhesive has been found to be Aerolite 306 with the resin applied to the wood
skin and the hardener to the honeycomb. A very close second to Aerolite is LePages P.V.A., this is certainly
easier to apply, particularly if run on the edges while honeycomb is compressed to the block stage,
before pinning down between surfaces. When the wing skins and honeycomb are dry and hard, the leading
edge strip should be glued in place and after the whole assembly is well and truly dry the wing may
be subjected to a "standing upon" examination to test it! One test specimen has had a weight of seventeen
stone on it (the heaviest man we could find!).
Optimum size to give maximum strength with lightest weight for our purposes seems to be a honeycomb
size of 3/4 in. or 1 in. across the flats of the hexagons. Anything smaller than this pushes the weight
up.
Bee keepers who keep extra large bees may welcome any left overs!
Price
varies with the size of the hexagons and the thickness, the smaller the honeycomb the higher the price
and, of course, the thicker material carries the higher price. As a general guide the size required
for model building would cost as little as 2 1/2 d. to 5 d. per sq. ft. (expanded) dependent on thickness
ranging from 1/4 in. to 1 in. depth.
Test pieces indicate that wings under about 36 in. span may be slightly heavier than conventional
methods of construction; but the strength is incomparable. A honeycomb with leading and trailing edge
of balsa but tissue-covered and doped would give good results with excellent airfoil maintenance, superior
to many standard surface spar methods.
Undercambered or symmetrical sections are no more difficult to make than the popular Clark Y with
its flat undersurface.
Try a double skin construction and amaze yourself.
Think of a C/L model which will last a couple of seasons with ease and remember that this form of
construction lends itself to components other than wings - why not fuselages, cowlings - even model
boxes?
Posted March 19, 2016
|