Scale modelers are always coming up with clever ideas for replicating intricate parts and assemblies that might earn
a few critical points from the judges. The "wow" factor is reportedly an important part of winning the hearts of those
who sit in judgment of your model. This "lost way" method of casting parts might be yet another tool in your arsenal.
According to the author, "lost-wax" casting dates back to ancient modelers and was used extensively during World War II
for high volume production of aircraft, ship, and land vehicles.
"Lost-Wax" Casting Goes Back to Ancient Modelers
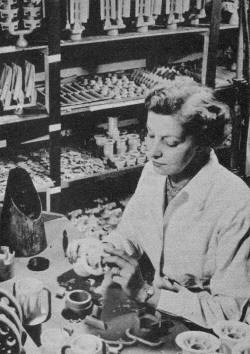 In
the early stages of World War II when the British were forced to step up production of blades for turbo-superchargers
the country's forging and machining resources were already stretched to maximum capacity. They adopted a casting method
so old its origin is shrouded in antiquity. It is known that early Chinese and Egyptian craftsmen used this process
known as "lost-wax" casting.
This is a procedure where an item modeled in wax is coated with a refractory "slurry" which sets at room temperature
to form a mold. The mold is then heated to melt out the wax; afterwards it is baked hard. Finally, molten metal is
poured into the cavity previously filled by the wax pattern and permitted to cool. Remove mold; there's your finished
product!
When you go into mass production, though, the process requires another, earlier step. This is the making of an
accurate metal die into which liquid wax may be injected to produce the pattern in quantity.
These
photos from the de Havilland Company's foundry show (top-left) a lady inspector with a swirler vane assembly made
of wax in two sections. In the background is a varied collection of intricate wax patterns.
Top-right photo: "Primary investment" comes by dipping the wax assembly into this "slurry" of fine refractory particles
in a liquid binder. When the wax is melted and drains away, this coating remains as a shell to form a smooth, hard
surface of the mold.
Photo right: Finished products are these castings which have complicated internal details that could not be fabricated
in one piece by any other means. These have not been machined after casting, yet note the detail and finish. Swirler
vane is at left.
Posted June 7, 2014
|